Empa researchers are working on producing artificial muscles that can keep up with the real thing. They have now developed a method of producing the soft and elastic yet powerful structures using 3D printing.
One day, these could be used in medicine or robotics—and anywhere else where things need to move at the touch of a button. The work is published in the journal Advanced Materials Technologies.
Artificial muscles don’t just get robots moving: One day, they could support people at work or when walking, or replace injured muscle tissue. However, developing artificial muscles that can compare to the real thing is a major technical challenge.
In order to keep up with their biological counterparts, artificial muscles must not only be powerful, but also elastic and soft. At their core, artificial muscles are so-called actuators: Components that convert electrical impulses into movement. Actuators are used wherever something moves at the push of a button, whether at home, in a car engine or in highly developed industrial plants. However, these hard mechanical components do not have much in common with muscles just yet.
Reconciling contradictions
A team of researchers from Empa’s Laboratory for Functional Polymers is working on actuators made of soft materials. Now, for the first time, they have developed a method for producing such complex components using a 3D printer.
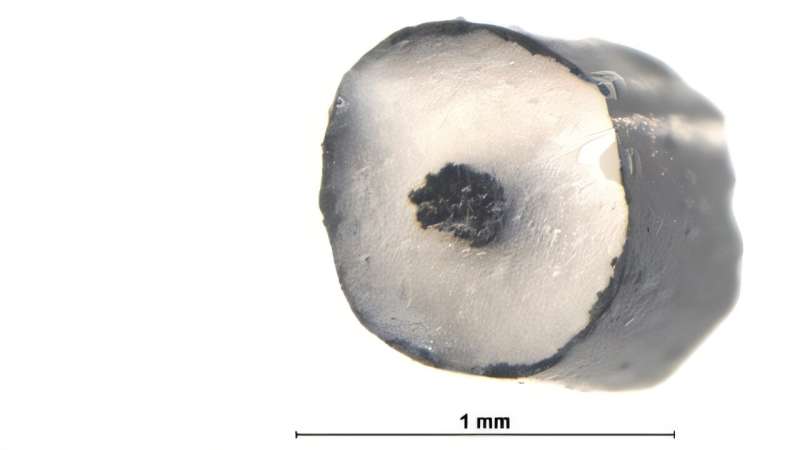
The dielectric elastic actuators (DEA) consist of two different silicone-based materials: a conductive electrode material and a non-conductive dielectric. These materials interlock in layers. “It’s a bit like interlacing your fingers,” explains Empa researcher Patrick Danner. If an electrical voltage is applied to the electrodes, the actuator contracts like a muscle. When the voltage is switched off, it relaxes to its original position.
3D printing such a structure is not trivial, Danner knows. Despite their very different electrical properties, the two soft materials should behave very similarly during the printing process. They should not mix but must still hold together in the finished actuator.
The printed “muscles” must be as soft as possible so that an electrical stimulus can cause the required deformation. Added to this are the requirements that all 3D printable materials must fulfill: They must liquefy under pressure so that they can be extruded out of the printer nozzle. Immediately thereafter, however, they should be viscous enough to retain the printed shape.
“These properties are often in direct contradiction,” says Danner. “If you optimize one of them, three others change … usually for the worse.”
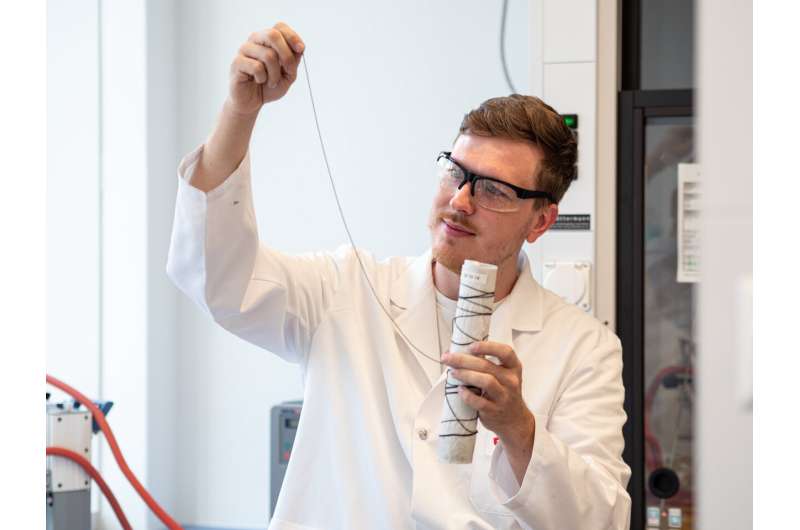
From a VR glove to a beating heart
In collaboration with researchers from ETH Zurich, Danner and Dorina Opris, who leads the research group Functional Polymeric Materials, have succeeded in reconciling many of these contradictory properties. Two special inks, developed at Empa, are printed into functioning soft actuators using a nozzle developed by ETH researchers Tazio Pleij and Jan Vermant.
The collaboration is part of the large-scale project Manufhaptics, which is part of the ETH Domain’s strategic area Advanced Manufacturing. The aim of the project is to develop a glove that makes virtual worlds tangible. The artificial muscles are designed to simulate the gripping of objects through resistance.
However, there are far more potential applications for soft actuators. They are light, noiseless and, thanks to the new 3D printing process, can be shaped as required. They could replace conventional actuators in cars, machinery and robotics. If they are developed even further, they could also be used for medical applications.
Opris and Danner are already working on it. Their new process can be used to print not only complex shapes, but also long elastic fibers. “If we manage to make them just a little thinner, we can get pretty close to how real muscle fibers work,” says Opris. The researcher believes that in the future it may be possible to print an entire heart from these fibers. However, there is still a lot to do before such a dream becomes a reality.
More information:
Patrick M. Danner et al, Rapid Manufacturing of High‐Permittivity Dielectric Elastomer Actuator Fibers, Advanced Materials Technologies (2025). DOI: 10.1002/admt.202500190
Citation:
Developing 3D-printed soft material actuators that can mimic real muscles (2025, March 11)
retrieved 11 March 2025
from https://techxplore.com/news/2025-03-3d-soft-material-actuators-mimic.html
This document is subject to copyright. Apart from any fair dealing for the purpose of private study or research, no
part may be reproduced without the written permission. The content is provided for information purposes only.