When the wind hits an obstacle, it flows around it and creates a low-pressure zone on the other side, known as a “windwake.” This flow becomes clear in observing desert sand.
“The same thing happens around offshore platforms. This means that the best place to measure the total methane emissions is not on the platform itself or very close by, but where the wind connects again. That’s often over a hundred meters away,” says Daniel Krause at SINTEF.
Based on this understanding, researchers have developed a new drone-based measurement strategy that makes it possible to detect and reduce methane emissions—often almost overnight.
The method is based on a deeper understanding of methane’s behavior and has already yielded major results.
“When the measurement method was tested on the Gjøa platform, which is owned by Vår Energi, we discovered a methane gas leak that corresponds to an annual emission of 100 metric tons,” says Krause.
The measurement method was developed by SINTEF through the LowEmission research center.
“It took no more than a week for Vår Energi to carry out the necessary repairs and reduce its emissions by a full 98%. The method has huge potential, and we’re pleased that other operators can also use it now,” says Krause. He is a research engineer at SINTEF and has been involved in developing the technology.
Up to now, it has been challenging to monitor overall methane emissions from oil platforms, as leaks can come from varied and scattered sources. The researchers have now gained a deeper understanding of the wind conditions around platforms, and discovered that it is possible to combine measurements from the scattered sources at one point, more than 100 meters from the platform. Measuring the emissions at a single point provides a more comprehensive understanding of the total emissions, allowing for more targeted work to reduce them.
The method is now freely available to all operators, both within and outside Norway. The method describes the procedure in enough detail for operators to be able to use it.
How important is it to solve this problem, and what makes this new technology so innovative?
Methane is the second-largest driver of climate change after CO₂. Although it has a much shorter lifetime in the atmosphere—around 12 years, compared to several centuries for CO₂—methane emissions heat the atmosphere much faster. Methane accounts for about a third of global warming today, and methane concentrations in the atmosphere have increased sharply over the past decade.
That is why authorities around the world are working on new laws to combat emissions, such as a new EU regulation to reduce methane emissions in the energy sector and several upcoming ones that are part of the EU’s Fit for 55 climate package.
The methane regulation places strict requirements on oil and gas production for accurately reporting and repairing leaks to cut methane emissions. There’s just one problem: we don’t actually know how much methane is being released.
“The biggest challenge for offshore operators is to obtain frequent and precise enough measurements of methane emissions that provide practically applicable information—how much methane is being emitted and from which sources,” says Krause.
He says that many existing measurement methods have significant uncertainty and provide a limited basis for decision-making. This in turn leads to fewer emission reductions. Without good reference measurements, it is difficult to understand the true extent of emissions—and without that insight, the opportunity to reduce them is limited.
“After all, you can’t stop a leak that you don’t know exists,” says Krause.
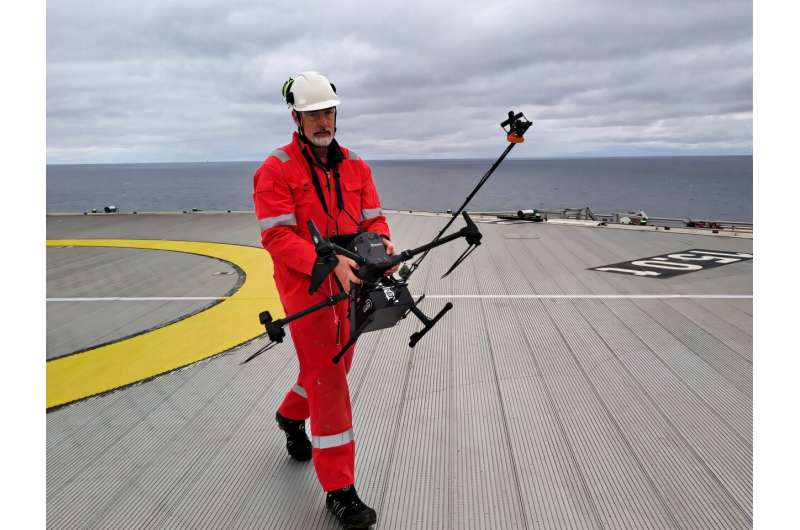
Combined drone and sensor technology
“Using drones to measure emissions from offshore platforms is nothing new. The innovation lies in where and how we carry out these measurements—and how we integrate them with measurements made directly on the platform,” the research engineer says.
As mentioned, methane leaks can come from a number of different sources on an offshore platform. While we can find and stop leaks by measuring specific emission sources, it is important to have a reference point—a place where the total amount of emissions can be determined. This will tell us whether all significant leaks have been detected or if any remain.
The researchers therefore equipped a DJI M600 Pro drone with a Trisonica wind sensor and an ABB LGR HoverGuard methane gas and CO₂ sensor adapted to the drone.
“Based on our understanding of the role of wind, we fly the drone in a tailored scanning pattern, a so-called ‘flux plane,’ in the areas where the emissions collect and pass through. This ensures more precise and reliable measurements,” Krause says.
The drone measurements are then compared to direct measurements from sources on the platform, both from emission sources already known to the operator and from what Krause measures. This includes sampling the produced water, measuring gas turbine exhaust and effective leak detection and repair (LDAR).
That is exactly how Krause discovered the 100-metric-ton-per-year leak on Vår Energi’s platform—a leak that was fixed within a week.
The next step is to simplify these improved measurement methods through remote control or autonomous flights. The simpler the measurements, the more easily they can be carried out, leading to a better understanding of emissions and a faster turnaround in reducing them. In the future, this procedure will hopefully be as easy as pressing a button.
Citation:
Drone-based method detects major methane leaks—the good news is that many can be repaired quickly (2025, May 20)
retrieved 21 May 2025
from https://techxplore.com/news/2025-05-drone-based-method-major-methane.html
This document is subject to copyright. Apart from any fair dealing for the purpose of private study or research, no
part may be reproduced without the written permission. The content is provided for information purposes only.