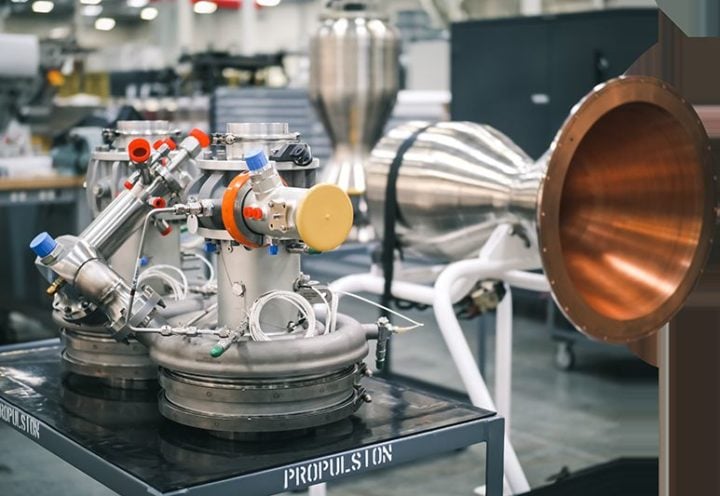
These turbopumps are used in the NewtonThree engine from the first stage of Virgin Orbit’s LauncherOne rocket. Produced by Barber-Nichols and similar in design and principle to pumps originally made for NASA, the pumps move liquid fuel into a rocket engine that ignites after being dropped from an airplane. Image credit: Virgin Orbit
The turbocharger is well known to car aficionados, but a similar technology is also important to rocket scientists.
To launch satellites and astronauts into space, large rockets rely on liquid-fueled engines. Pumping propellants into these engines requires a lot of power, so this task is typically accomplished by turbopumps – high-speed pumps powered by turbines.
Turbopumps are similar in principle and design to the turbocharger, except turbopumps are more complex and can have 20 times more power density than the turbochargers found in a car. But both are examples of turbomachinery, rotating machines that transfer energy into a fluid or vice versa.

A Fastrac engine undergoes testing at Marshall Space Flight Center. The turbopump used in this design was manufactured by Barber-Nichols, which went on to produce similar designs for companies such as SpaceX. Image credit: NASA
In the 1990s, NASA recognized a need to improve costs and reduce development times for a new generation of spaceplanes that could take off from a larger aircraft, launch into suborbital space, and glide safely to the ground.
Through the X-34 program, the agency planned to develop a vehicle that would demonstrate these capabilities. To do so, it needed a new engine that could thrust the vehicle to great speeds incredibly quickly, and this required a brand-new turbopump.
NASA’s Marshall Space Flight Center in Huntsville, Alabama, contracted with Summa Technology to build the engine, dubbed Fastrac. Barber-Nichols Inc. of Arvada, Colorado, was subcontracted to build the engine’s turbopump. Barber-Nichols was no stranger to working with the space agency, but to make this particular pump, the company had to turn to a cutting-edge process.
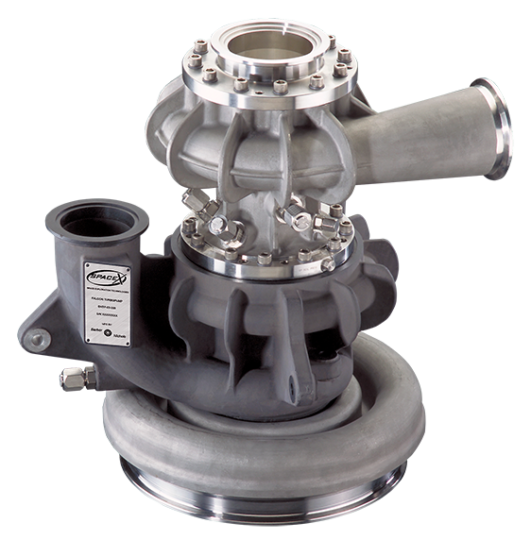
This turbopump, intended for the SpaceX Merlin engine, is one of many designs manufactured by Barber-Nichols. The company credits work it did on NASA’s Fastrac program with enabling better and cheaper methods of building these machines. Image credit: Barber-Nichols Inc.
“It’s really hard to machine supersonic turbine blades,” said Matt Marsh, Marshall Engine Components Development and Technology Branch chief. “It can be done with milling, but you’ve got to be really good at it if you’re doing something really small and precise.”
Instead of milling, Barber-Nichols manufactured the Fastrac turbopump using a process called electrochemical machining, in which material is successively stripped away using high-current electricity passed through an electrolyte.
While this was not a new process, applying it to the highly detailed work of building Fastrac’s turbopump turbines out of nickel superalloys made the job quicker and much cheaper than other methods while providing the precision and quality required for this turbopump.
Although the X-34 program never got off the ground, Barber-Nichols still produces turbopumps for rocket applications, and the company credits the work on Fastrac with helping to refine the electrochemical machining process.
“What we learned enabled us to have the expertise to design rocket engine turbopumps,” said Greg Forsha, senior staff engineer for Barber-Nichols. “One success has led to the next.”
Barber-Nichols’ turbopumps are found in rockets Virgin Orbit uses to fill a similar role to the X-34 plane the original Fastrac engine was intended for – launching to space from an airplane. Other companies have used these pumps as well, such as SpaceX’s Merlin engine, used to launch private satellites into orbit.
The work has found uses outside of aerospace as well, supporting exhaust heat energy recovery systems used in cars as well as geothermal power plants. Barber-Nichols’ new products are more than just machines, incorporating advances in electronic control systems.
“In the ’90s, we just did the mechanical side of things, now we cover all kinds of electronics,” said Forsha. “We’re a one-stop shop for that entire system.”
Source: NASA