Evolutionary robotics is a sub-field of robotics aimed at developing artificial “organisms” that can improve their capabilities and body configuration in response to their surroundings, just as humans and animals evolve, adapting their skills and appearance over time. A growing number of roboticists have been trying to develop these evolvable robotic systems, leveraging recent artificial intelligence (AI) advances.
A key challenge in this field is to effectively transfer robots from simulations to real-world environments without compromising their performance and abilities. A paper by researchers at University of York, Edinburgh Napier University, Vrije Universiteit Amsterdam, University of the West of England and University of Sunderland, published in Frontiers in Robotics and AI, investigated the impact that hardware can have on the development space of evolvable robots.
“One of the greatest challenges for evolutionary robotics is bringing it into the hardware space and creating real, useful robots,” Mike Angus, a research engineer who designed hardware for the study, told Tech Xplore.
“The ARE project sought to advance this aim with an ambitious hybrid ecosystem combining both simulated and autonomously fabricated robots. The robots were built using a novel semi-modular approach in which the robot bodies were 3D printed and equipped with sensors and actuators in the form of modular ‘organs,’ aiming for a much richer morphological space than previous work in hardware robot evolution.”
The recent paper by Angus and his colleagues was inspired by two key observations. The first is that so far very few past studies in evolutionary robotics have explored the technical details associated with the physical implementation of evolvable robots in depth. The second is that these technical details are so crucial to the real-world performance of evolutionary systems, that they are definitely worth further investigation.
“In the process of developing our hardware platform for evolving robots, we discovered that the interplay between the evolutionary processes and hardware implementation is highly complex, such that neither can be designed effectively without detailed consideration of the other,” Angus explained.
“The primary objective of the paper was therefore to bring together these two worlds, sharing a technical specialist’s perspective on the hardware design, juxtaposed with the observed effects of those design decisions on the evolutionary process, to highlight how every aspect of the hardware implementation can have an effect on the evolutionary space.”
Angus and his colleagues designed a new evolutionary robotics platform with which diverse robot “phenotypes” could be fully manufactured using autonomous techniques, in particular 3D printing. This system would allow the development of different “species” of robots, with a wide range of morphologies and body structures, without the need to manually assemble many robot generations, which would be both costly and time-consuming.
Ultimately, the team came up with a semi-modular architecture that combines a 3D printed, free-form plastic skeleton with clip-on modular “organs.” These organs provide the robot with its essential functionality such as movement, sensing, processing and power.
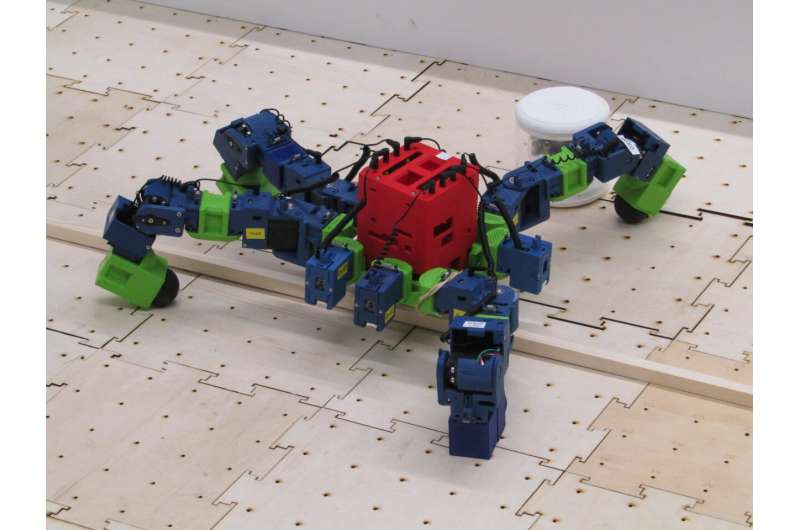
“The body shape and organ configuration in our architecture is defined generatively by a compositional pattern-producing network (CPPN), the parameters of which are then evolved,” Angus said.
“A great deal of work went into creating a system that could actually build such robots, because there are innumerable practical challenges to contend with, from the 3D printing process itself, to the automated assembly process, the mechanical and electrical interconnections, and the underlying electronics required to perform reliably in a wide range of different robot configurations. All this resulted in a system that was very much defined by the methods used to address these practical challenges.”
When they investigated the performance of their proposed system, Angus and his colleagues discovered that the exploration space it enabled for evolving robots was quite limited and difficult to navigate, because physical constraints made many of the evolved designs unviable. They thus also realized that they needed additional methods to reliably ensure the feasibility of robots in the evolving population, the results of which would in turn further impact the overall success of the evolutionary process.
In their paper, the researchers conceptualized this problem with what they refer to as the “viable phenotype space.” This term refers to the understanding of how the exploration space of an evolvable robot platform’s possibilities is affected by constraints set by its hardware implementation.
“Much of evolutionary robotics research relies on simulation, where hardware constraints are easily omitted, and experiments with physical implementations of evolved robots have tended to be relatively simple in morphological structure, such that the ‘viable phenotype space’ is still relatively straightforward to explore,” Angus said.
“However, this principle can be expected to become increasingly significant as we try to bring evolutionary robotics towards solving practical problems in the real world, where the challenges are more complex. The ‘viable phenotype space’ determines not only the potential usefulness of the evolved robots, but also the difficulty of the problem faced by evolution as it attempts to discover the best robot body plans.”
The recent work by Angus and his colleagues introduces a new idea that could guide the development of new evolutionary robotics systems, helping researchers to ensure that they will perform well in the real world. Fundamentally, the team’s observations suggest that the development of effective evolutionary robotic systems highly depends on their creators’ ability to consciously shape their “viable phenotype space.”
This space should be aligned with the tasks and missions that specific robots are designed to tackle. In addition, evolutionary algorithms underpinning the robots should be effectively adapted to make sure that they perform well in the identified space.
Essentially, Angus and his colleagues showed that if evolutionary roboticists employ conventional design approaches when creating both hardware and evolutionary algorithms for their systems, their ability to evolve practical robots will be very limited. By following their proposed principles and theoretical perspective, on the other hand, they could be able to create more adaptive and highly-performing evolved robots.
“There are three possible directions for our future research, all of them with the objective to enable evolutionary algorithms to operate within the viable phenotype space more effectively,” Edgar Buchanan Berumen, co-author of the paper, said.
“We would like to develop a new methodology to aid evolutionary roboticists in designing robot platforms in the right way to reduce the hardware limitations in the evolution landscape. The second direction involves designing a genotype representation that allows evolution to maximize the number of feasible and diverse morphologies. The third direction is a study to analyze and identify the best constraint-handling strategy to aid the evolutionary algorithm to traverse the viable phenotype space.”
More information:
Mike Angus et al, Practical hardware for evolvable robots, Frontiers in Robotics and AI (2023). DOI: 10.3389/frobt.2023.1206055
© 2023 Science X Network
Citation:
Exploring the effects of hardware implementation on the exploration space of evolvable robots (2023, September 4)
retrieved 4 September 2023
from https://techxplore.com/news/2023-09-exploring-effects-hardware-exploration-space.html
This document is subject to copyright. Apart from any fair dealing for the purpose of private study or research, no
part may be reproduced without the written permission. The content is provided for information purposes only.